Static electricity can damage LEDs at any time from manufacturing to use. Static electricity release must be properly handled during the manufacturing and use of LEDs. It was found that the anti-static human body model of LED chips with SiC as the substrate can reach more than 1100V, while the static electricity of LED chips with sapphire as the substrate can only reach 400-500V. Such low anti-static ability has brought great inconvenience to LED packaging manufacturers and application manufacturers. When LED chips are injured by static electricity, black spots will form on their surface, and these black spots will no longer emit light. Therefore, the degree of damage to the chip is different, and its performance is also different. Minor injuries may not be visible on the surface, but the brightness will be reduced and attenuated by a small amount, and the IR value (reverse current) will increase; for moderately injured chips, the tube voltage drop will increase significantly (from the conventional 2.8V-3.3V to more than 4.0V-5.5V), the brightness will decrease significantly (less than 50% of the original normal brightness), and the IR will increase, which will seriously affect the life of the LED, gradually lose its function during use, and may eventually cause a dead light. Therefore, whether static electricity is properly prevented in industrial production directly affects the product yield, reliability and even the economic benefits of the enterprise, so static electricity prevention technical measures are crucial.
Research data shows that static electricity above 1500V will immediately cause serious damage to the LED. In the autumn and winter seasons in the north, the static electricity of the human body is about 1000V-1500V, so direct contact with the human body can easily cause damage to the LED. Compared with previous years, this winter’s precipitation is less, the environmental humidity is greatly reduced, and the hidden dangers of static electricity are comparable to those in the north. Therefore, in the production process, no matter the environment, facilities, operators and other links, appropriate preventive measures must be taken:
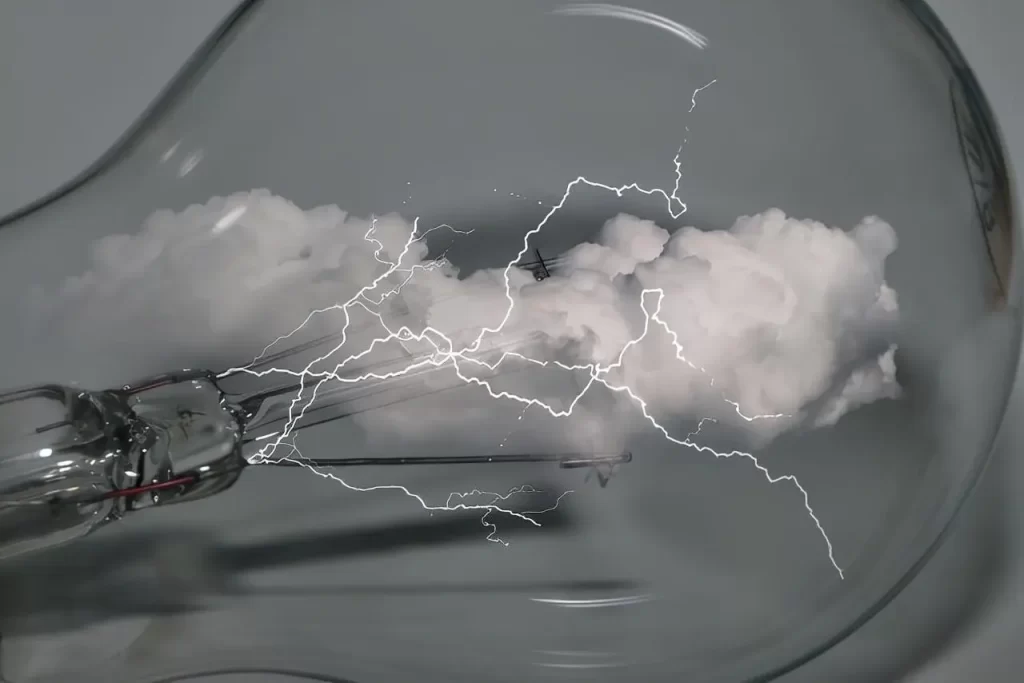
- Do a good job of static discharge in the production environment
The workbench, soldering iron, foot cutting machine, automatic reflow soldering and other equipment in the production environment and even the entire factory are grounded. The grounding body is generally made of angle steel and steel pipe. Galvanized steel should be used in corrosive soil. Its length is between 2-3m, and the vertical depth of the ground is not less than 2m. The grounding wire uses an insulated copper wire greater than 1.5mm2 and less than 25mm2.
- Ensure that the workshop production equipment and the surrounding environment meet the anti-static requirements
2.1 The workbench must use an anti-static mat and be grounded. The green surface of the anti-static rubber is the anti-static generating layer, which has a large resistance and a surface resistance of 100MΩ~100,000MΩ. It can be connected by a buckle type, grounded by a special anti-static wristband wire (containing a 1MΩ resistor), or a 0.2mm thick iron plate or copper foil is placed on the insulating table, and the wire is welded to the static ground wire through a 1MΩ resistor, and then the anti-static rubber is flattened (black side down, close to the conductive sheet). The 1MΩ resistor also provides a static discharge path to prevent over-speed discharge and sparking and isolation. Seats should also be taken seriously. Most production lines use ordinary plastic stools, which are very easy to generate static electricity by friction with clothes. If conditions permit, anti-static chairs should be used and connected to the static ground through a 1MΩ resistor. At least the plastic stools should be covered with anti-static cloth. The anti-static floor is a composite structure similar to anti-static rubber. The lower layer is a conductive layer connected to the anti-static ground, and the upper layer is an insulating anti-static generating layer. It will not generate static electricity due to the friction of walking. When laying, the conductive layer should be separated from the ground and walls of the building with an insulating mat to prevent the floor from carrying static electricity when struck by lightning, and the conductive layer should be connected to the anti-static ground through a 1MΩ20W resistor to play an electrostatic shielding role. Generally, electronic factories use simple anti-static floors (only an insulating anti-static generating layer, mostly coatings or floor glue), which are directly laid on the ground of the building, greatly reducing the cost, and can also prevent static electricity generated by walking, but the protection against ultra-high voltage static induction and strong electromagnetic induction generated by lightning is poor.
2.2 Antistatic component boxes are required for LEDs.
2.3 Soldering irons, lead cutting machines, reflow soldering and other equipment must be grounded.
2.4 PCBs on the assembly line (mainly DIP post-soldering, testing, assembly and other processes) should be covered with antistatic sponge pads to prevent static electricity and board scratches. Antistatic board storage and transportation vehicles or card boxes (with surface resistance below 106Ω) should be used for transportation between processes, and the static ground should be properly connected through a 1MΩ resistor.
2.5 The impact of ambient temperature and humidity on static electricity: Electronic operations, especially SMT, have high requirements for temperature and humidity. The temperature can be controlled at 18~28℃. Too high or too low will affect the normal operation and accuracy of the equipment. The relative humidity should be between 50% and 85%. Too low will easily generate static electricity. Too high equipment is prone to condensation and the water content of solder paste increases, so monitoring and regulation should be strengthened. For anti-static, when the relative humidity is low in autumn and winter, a humidifier or wet cloth mopping method can be used to solve it.
2.6 Install ion fans: The temperature of the preheating part of the wave furnace is 80~120℃. It is very easy to generate static electricity under such high temperature and dry hot air. The ion fan ionizes the air into positive and negative ions by high pressure, and blows the air containing a large amount of positive and negative ions into the furnace by the fan to neutralize the static electricity generated by high temperature and hot air on the PCB and components. Therefore, an ion fan should be installed at the entrance of the wave furnace. Ion fans can also be installed at the entrance of the anti-static work area, the starting point or the top of the conveyor belt according to actual needs.
3 Ensure the implementation of human protection measures
Wear anti-static clothing, so-called anti-static clothing, is a fabric woven with special synthetic fibers. The correct way to wear it is to wear only a shirt or underwear inside and anti-static clothing outside. Wearing multiple pieces of chemical fiber and wool clothing inside and anti-static clothing outside in winter is of little use; anti-static gloves play multiple roles in preventing static electricity, isolating hands from contacting products (insulation), and preventing sweat stains from contaminating products, and are necessary; anti-static wrist straps are made of a stainless steel shell that fits close to the wrist and is grounded by a wire and an iron clamp through a 1MΩ resistor inside the line. The purpose is to discharge static electricity on the human body at any time, prevent sparks generated by rapid discharge from damaging the LED, and play an isolation role. The so-called wireless bracelet does not actually discharge the static charge carried by the human body.
3.1 Standardize the wearing and clamping methods of anti-static wrist straps:
3.1.1 The stainless steel shell of the anti-static wrist strap should be worn on the inside of the left wrist, where the contact resistance is the smallest.
3.1.2 It should be in close contact with the skin, not loose, and not separated by clothing.
3.1.3 The crocodile clip should clamp the exposed part of the static ground wire at the root, and should not be clamped with the front teeth.
3.1.4 When walking, the operator should remove the clip and wrap the connection line around the wrist for mobile use.
3.2 The anti-static wrist strap should be tested and recorded once in the morning and afternoon of each shift. The tightness shall be based on the test. If it fails, it shall be adjusted or replaced immediately.
4 Others
4.1 The electric soldering iron should be an anti-static low-voltage constant-temperature soldering iron and well grounded.
4.2 Use a low-voltage DC electric screwdriver with a grounding wire.
4.3 Anti-static brushes should be used for small-batch cleaning of PCBs, and ordinary plastic brushes should not be used.
4.4 Anti-static materials should be used for ceilings and walls where necessary. Ordinary gypsum boards and lime paint walls are also acceptable, but plastic ceilings and ordinary wallpapers and plastic wallpapers are prohibited.
4.5 During the operation, avoid touching the pins of the light-emitting tube directly, and hold the tube holder or the lamp body when taking it out.
5 Supervision and measures for anti-static
5.1 Electrostatic tester: If conditions permit, consider adding a “handheld non-contact electrostatic tester” so that the static situation can be monitored in real time, but because it is too expensive, most companies dare not ask for it.
5.2 Monitoring and recording: Anti-static measures must be implemented by a dedicated person and a system must be formed to truly implement them, otherwise all hardware investment may not play a practical role.
5.2.1 Personnel: Two people should be responsible for part-time management, testing and recording.
5.2.2 Testing and recording: In summary, the following tests and records should be completed every day.
a. Electrostatic test point – static ground, use a pointer multimeter to measure resistance
Electrostatic ground – equipment ground, use a pointer multimeter to measure resistance
b. Electric soldering iron head grounding, soldering iron tip temperature measurement, use a pointer multimeter, thermometer
c. Small tin furnace grounding, tin furnace temperature measurement, use a pointer multimeter, thermometer
d. Equipment instrument grounding measurement, use a multimeter
e. Electrostatic wrist strap grounding test, use an electrostatic wristband tester
f. Indoor temperature, relative humidity measurement and control, thermometer/hygrometer
5.2.3. Check the dress of staff in the anti-static work area and the implementation of various anti-static regulations.
5.2.4. If conditions permit, use an electrostatic tester to measure the electrostatic voltage under various conditions at the work site and on the assembly line. The electrostatic voltage should generally be less than 100V, and less than 25V in special cases.
5.3. Training and literacy: Anti-static knowledge and measures should be taken as an important part of all-staff training so that every employee can understand and form good professional habits. Plastic boxes, leather, cardboard, glass and other debris that are prone to static electricity are not allowed to be piled on the anti-static safety workbench. Operators and those who need to touch the LED should wear anti-static wrist straps and gloves before touching it.
5.4 Measurement: Use the resistance range of the pointer multimeter to measure the resistance between each anti-static test point and the anti-static ground wire, 5~15Ω. Ideally, it should be 0Ω, but the actual measured value is the sum of the resistance of the 2mm2 wire from the test point to the summing point + the resistance of the 6mm2 wire from the summing point to the measured point. This value is about 5-15Ω and basically unchanged. If the measurement result tends to infinity, it is considered that the anti-static ground wire or the measuring line has a broken wire, which should be repaired in time.
References:
[1] “Practical Handbook of Electrical and Electronic Engineering” edited by Liu Guangyuan, Electronic Industry Press.
[2] “LED Manufacturing Technology and Application” edited by Chen Yuandeng, Electronic Industry Press.
[3] “LED Drive Circuit Design and Application” edited by Zhou Zhimin, Zhou Jihai, Ji Aihua, People’s Posts and Telecommunications Press.